The Black Diamond Story
I’m Dean Jenkins, founder of Black Diamond Solutions, LLC, and inventor of “Black Diamond Flexible Sanding Blocks.”
For my latest “Resto-Mod” project, a 1968 Chevrolet el Camino, I decided to attempt the body and paint work myself.
After way too many hours on YouTube and other sites, I finally came across the Southern Polyurethane (SPI) user forum. FYI, in my opinion, that is the best body and paint forum on the internet, hands down.
I read many, many discussions about sanding blocks. I noticed that several people were talking about the benefits of using acrylic or polycarbonate bases for sanding blocks.
The benefits of using those materials were that the actual sanding surface was “rock hard,” which resulted in making it easier to get the surface absolutely flat and smooth. In addition, the acrylic/poly could flex and conform to a crowned surface, making it possible to get a curved door, fender, hood, roof, etc. flat and smooth, across the surface contour, much quicker and easier.
But the problem was attaching a handle to the acrylic/poly. Several people posted pictures of their home-made solutions with tape, PVC pipe taped on, etc. These worked, sort of, but were awkward and wore out quickly.
And, if you wanted different degrees of flexibility, you had to get different thicknesses’ of acrylic/poly and make several tools for each desired length.
I found that a handful of vendors were starting to offer acrylic/poly-based sanding blocks, but they had the same problem – awkward handles and you had to get a large set of multiple tools to get different degrees of flex. And they were expensive!
In my research, I found that there had been a previous product, AFS Flexible Sanding Blocks, that people loved! It had a thin stainless-steel base, a nice, ergonomic foam rubber handle, and it’s flexibility could be adjusted by inserting a series of steel rods in the tool. The drawback to these blocks was that the stainless-steel base was very thin and would yield to imperfections in the surface being sanded, unlike an acrylic/poly base. And, the design was pretty complex, with lots of internal clips for the rods, which over time wore out and then the rods would slip out while you were sanding. And it seemed difficult to manufacture economically. Also, unfortunately, the inventor of these blocks passed away and the company went out of business.
** I offer full recognition and gratitude to John W. Wheeler, the inventor of the AFS Flexible Sanding Blocks. His work inspired my ideas and I “stand on his shoulders.” For those who wonder if I am infringing on the patent for his work, the answer is no. His patent, US6544113B1, has expired.
And, with the help of a patent attorney, I was able to demonstrate significant differentiation in my design and to be granted patent pending status; EFS ID: 46082295, which is expected to receive full patent approval in 2023.
I started exploring what it would take to build on the idea of the flexibility of the AFS blocks, to capture the benefits of an acrylic/poly base, and to improve and simplify the design and manufacturability with some of the current materials and processes now available.
I began working on this in the Spring of 2022 and started a discussion thread on the SPI forum to gather input and feedback from real users. The response, support and helpful suggestions has been nothing short of amazing! Click Here for that thread.
After nearly a year of research, design, prototyping and trial and error, I am preparing to launch the initial set of “Black Diamond Flexible Sanding Blocks.”
This has been a fun and rewarding journey! I hope these products are commercially successful and that they truly do help you “lay down some glass,” faster, easier, and better. And I hope to build on the initial products and offer an expanded line of tools in the near future.
What I saw . . .
Tape handles on plexiglas
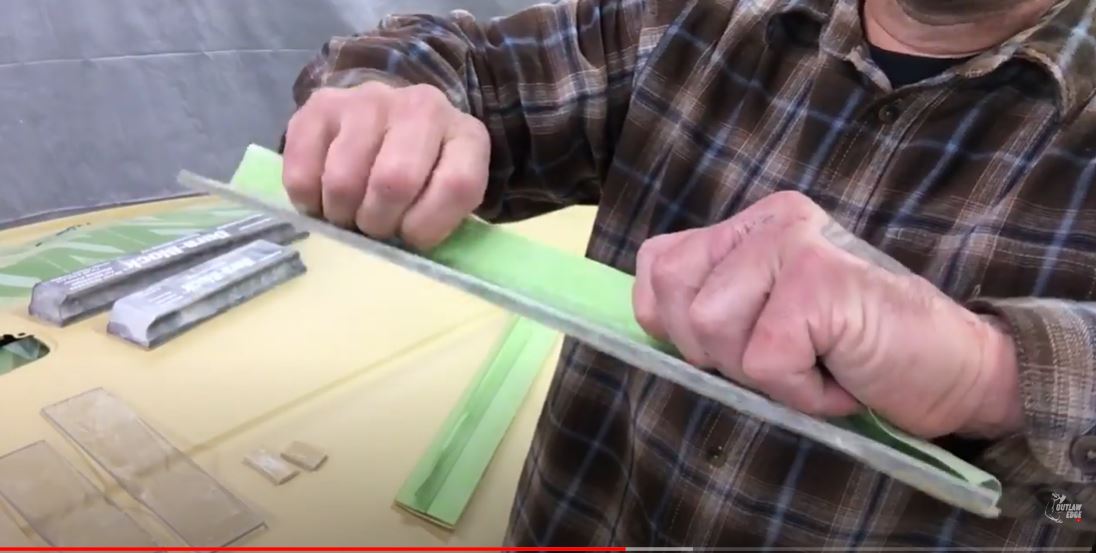
Initial handle drawings
(These changed . . .)
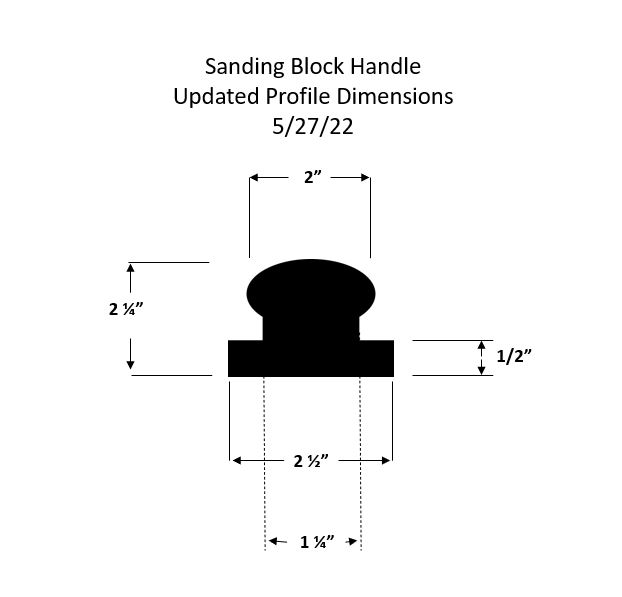